Commonly used blanks for machining include castings, forgings, profiles and welded parts. Different types of blanks and the accuracy, roughness and hardness of the blanks have a direct impact on the machining process.
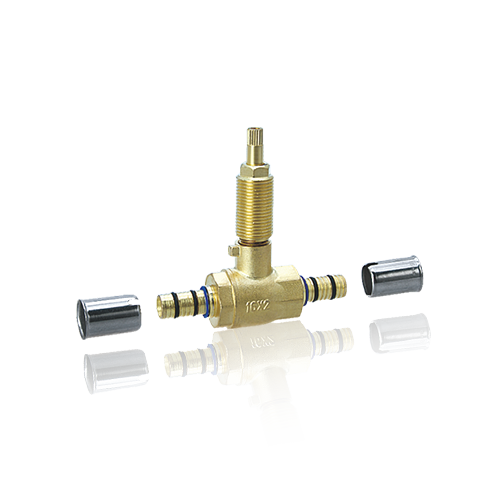
The following factors should be considered when selecting valve blanks.
1. The material of the part and the organization and performance requirements of the material. The part material specified on the design drawing generally determines the type of blank. For example, if the part material is cast iron, the casting method must be used to make the blank. For steel parts, the mechanical properties of the material should be considered when selecting the blank. For example, the parts of high-pressure valves should generally be forged or welded to ensure that the material has good mechanical properties.
2. The structural shape and external dimensions of the parts. The structural shape of the part is an important factor that affects the selection of the blank. For example, a valve body with a complex structure and shape can choose a casting. The valve body with a large size can be cast by sand casting; the valve body with a small size can be cast by investment casting.
3. The size of the production program. The larger the production program of the parts, the better the economic effect of using high-precision and high-efficiency blank manufacturing methods.
4. Conditions for blank manufacturing. The blank should be selected according to the on-site equipment status and technological level, and the development prospects should be considered, and advanced blank manufacturing methods should be gradually adopted.
Machining allowance and its determination method
(1) Basic concepts
1. Total machining allowance and process allowance
(1) The difference between the total machining allowance blank size and the design size of the part drawing.
(2) Process allowance The difference between the dimensions of two adjacent processes·
(3) Basic allowance The difference between the basic dimensions of the blank and the corresponding basic dimensions on the part drawing, and the difference between the basic dimensions of two adjacent processes, are respectively called the basic machining allowance (}boj) and the basic process allowance (Zbj) a
In the formula, n——the number of processes or steps.
2. Single-sided margin and double-sided margin
(1) For rotary surface processing, the single-side allowance refers to the radius difference between two adjacent processes, and the double-sided allowance refers to the diameter difference between two adjacent processes, in order: zb.2zb. Express. Generally, double-sided (diameter) margin is used.
(2) For plane machining, the single-sided allowance refers to the difference in dimensions between two adjacent processes when processing one surface on the other surface. The double-sided allowance refers to the simultaneous processing of two surfaces on the basis of the symmetry plane of the machined surface The size difference between two adjacent processes