The sealing surface of the closing part of the control valve is one of the important working surfaces of the valve. Whether the material selection is reasonable and its quality status directly affect the function and life of the control valve.
Working conditions of the sealing surface of the regulating valve
Due to the wide range of uses of regulating valves, the operating conditions of the sealing surfaces vary widely. The working pressure can range from vacuum to ultra-high pressure; the working temperature can be from -296 to 816 °C, and in some cases, the working temperature can reach 1200 °C; the working medium can range from non-corrosive media to strong corrosive media such as various acid and alkali. From the perspective of the force of the sealing surface, it is subjected to extrusion force and shear force; from the perspective of tribology, there are abrasive wear, corrosion wear, surface fatigue wear, erosion and so on. Therefore, the suitable sealing surface material should be selected according to different working conditions.
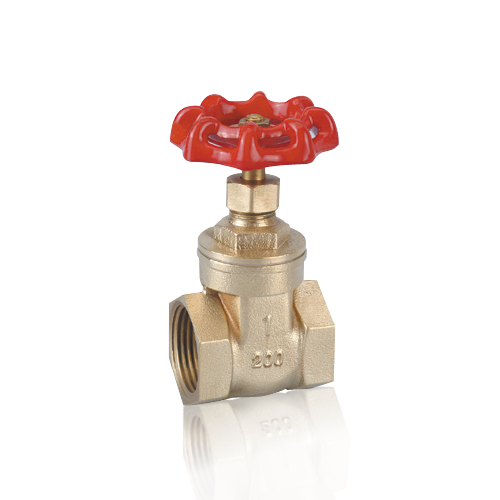
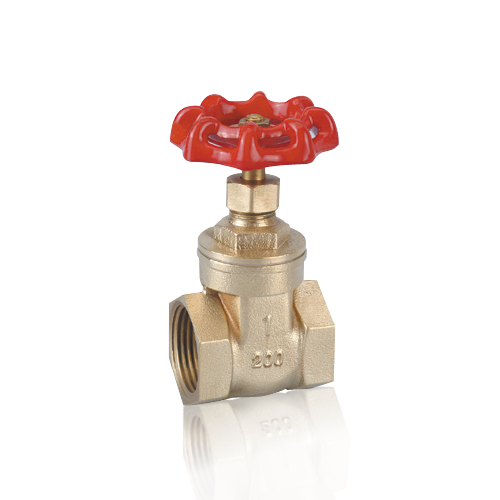
(1) Abrasive wear This is the wear that occurs when a rough hard surface slides on a soft surface. Wear that occurs when a hard material is pressed into a surface of a softer material, sliding over a soft surface. Hard material is pressed into the surface of the softer material, creating a tiny groove in the contact surface. The material shed by this groove is pushed away from the surface of the object in the form of debris or loose particles.
(2) When the surface of the metal is corroded by abrasive wear, a layer of oxide is produced. This layer of oxide usually coats the area affected by corrosion, which slows down further corrosion of the metal. However, if slippage occurs, the surface oxide is removed and the exposed metal surface is subject to further corrosion.
(2) When the surface of the metal is corroded by abrasive wear, a layer of oxide is produced. This layer of oxide usually coats the area affected by corrosion, which slows down further corrosion of the metal. However, if slippage occurs, the surface oxide is removed and the exposed metal surface is subject to further corrosion.
(3) Repeated cyclic loading and unloading of surface fatigue wear will cause fatigue cracks on the surface or subsurface, forming debris and pits on the surface, and eventually leading to surface damage.
(4) Erosion material damage is caused by the impact of sharp particles on the surface of the object. It is similar to abrasive wear, but with a rough surface.
(5) Scratch Scratch refers to the damage of the material caused by friction during the relative movement of the sealing surface.