Generally speaking, when the pressure is lower than PN40, from economic and technical considerations, it is more appropriate to use a floating ball, because in this case the ball is pushed to the outlet end and the pressure drop is very safe. Good seal. When the caliber is larger than DN150, the fixed ball valve is the most used.
This is because the mass of the ball of this caliber valve is very large, about 50kg or more. If a floating ball is used, the ball is pressed on the sealing seat, and the sealing seat will be greatly worn during operation.
On the contrary, the fixed ball seals along the axial direction of the flow channel, so that the seal seat will not be worn so much.
Ball valves with a pressure of PN50 and a diameter of DN50 or more also use fixed balls, because if a floating ball is used, the force exerted by the medium on the outlet sealing seat through the ball is calculated by the medium pressure on the area formed by the diameter of the flow channel. of. If a fixed ball is used, the pressure of the medium acts on the end face of the seal seat, and the pressing force between the ball and the seal seat produced by this force is much smaller than the former. In this way, the frictional force is reduced, the normal component force on the connecting surface of the ball and the valve stem is reduced, thereby the torque is reduced, the reliability is improved, and the service life is prolonged. It is also worth noting that foreign ball valves used in pipelines for oil, natural gas and flammable media are required to have fireproof structures and have been verified by fireproof tests. For ball valves used in vulcanization environments, materials that are resistant to vulcanization stress cracking (SSC) are also required. The performance parameters of commonly used ball valves are as follows: nominal size DN10~1400; nominal pressure PN16~420; working temperature ts600℃.
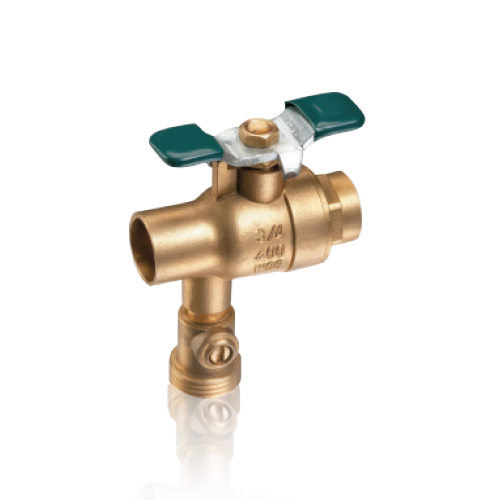
(2) Types of ball valves According to the structure, ball valves can be divided into the following types:
(3) The characteristics of the ball valve The ball valve is a valve developed on the basis of the plug valve, which has some advantages of the plug valve.
①The medium and small diameter ball valve has a simple structure, small size and light weight.
②The fluid resistance is small, and the fluid resistance of the ball valve is the smallest among all kinds of valves. This is because the cross-sectional area of the valve body channel, the ball channel and the connecting pipe are equal when fully opened, and they are connected in a straight line.
③It is quick and convenient to open and close, and the flow direction of the medium is not restricted.
④The opening and closing torque is smaller than that of the plug valve. This is because the contact area of the sealing surface of the ball valve is smaller, and the opening and closing is less labor-intensive than the plug valve.
⑤The sealing performance is better. This is because the material of the ball valve sealing ring is mostly plastic, and the friction factor is small; when the ball valve is fully opened, the sealing surface will not be eroded by the medium.